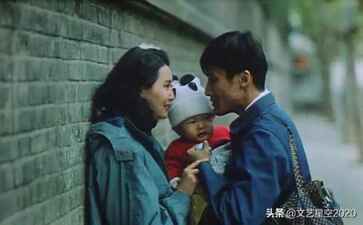
中山市萬家安電子科技有限公司位于固安縣,中山市萬家安電子科技有限公司www.nbaijia.com.cn經(jīng)營范圍含:供暖工程、服裝輔料、染料、黑色金屬制品、房產(chǎn)、玻璃生產(chǎn)加工機械、儀器、減速機、羊絨衫、種牛(依法須經(jīng)批準(zhǔn)的項目,經(jīng)相關(guān)部門批準(zhǔn)后方可開展經(jīng)營活動)。。
中山市萬家安電子科技有限公司將堅決貫徹黨中央、國務(wù)院關(guān)于深化國有企業(yè)改革的決策部署,緊密遵循國資委關(guān)于發(fā)展壯大企業(yè)的指導(dǎo)意見,堅定不移地推動企業(yè)改革進程。在此過程中,我們將進一步調(diào)整產(chǎn)業(yè)結(jié)構(gòu),優(yōu)化資源配置,以提升企業(yè)的核心競爭力為核心目標(biāo)。同時,我們將全面提升企業(yè)整體素質(zhì),不僅立足國內(nèi)市場,更要面向國際市場,以更加開放和進取的姿態(tài),向著更加宏偉的目標(biāo)奮勇前進,努力開創(chuàng)企業(yè)發(fā)展的新篇章。
中山市萬家安電子科技有限公司在發(fā)展中注重與業(yè)界人士合作交流,強強聯(lián)手,共同發(fā)展壯大。在客戶層面中力求廣泛 建立穩(wěn)定的客戶基礎(chǔ),業(yè)務(wù)范圍涵蓋了建筑業(yè)、設(shè)計業(yè)、工業(yè)、制造業(yè)、文化業(yè)、外商獨資 企業(yè)等領(lǐng)域,針對較為復(fù)雜、繁瑣的行業(yè)資質(zhì)注冊申請咨詢有著豐富的實操經(jīng)驗,分別滿足 不同行業(yè),為各企業(yè)盡其所能,為之提供合理、多方面的專業(yè)服務(wù)。
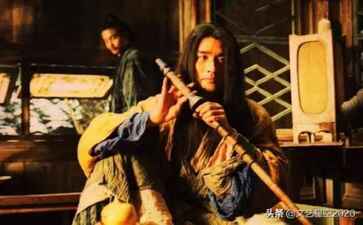
中山市萬家安電子科技有限公司秉承“質(zhì)量為本,服務(wù)社會”的原則,立足于高新技術(shù),科學(xué)管理,擁有現(xiàn)代化的生產(chǎn)、檢測及試驗設(shè)備,已建立起完善的產(chǎn)品結(jié)構(gòu)體系,產(chǎn)品品種,結(jié)構(gòu)體系完善,性能質(zhì)量穩(wěn)定。
中山市萬家安電子科技有限公司是一家具有完整生態(tài)鏈的企業(yè),它為客戶提供綜合的、專業(yè)現(xiàn)代化裝修解決方案。為消費者提供較優(yōu)質(zhì)的產(chǎn)品、較貼切的服務(wù)、較具競爭力的營銷模式。
核心價值:尊重、誠信、推崇、感恩、合作
經(jīng)營理念:客戶、誠信、專業(yè)、團隊、成功
服務(wù)理念:真誠、專業(yè)、精準(zhǔn)、周全、可靠
企業(yè)愿景:成為較受信任的創(chuàng)新性企業(yè)服務(wù)開放平臺
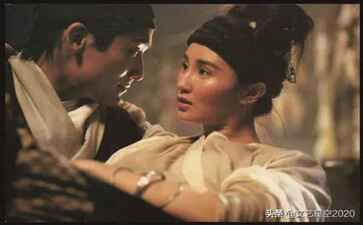